金屬軟管泄漏原因分析與預(yù)防
陳彩霞,王步美,陳楊
江蘇省特種設(shè)備安全監(jiān)督檢驗(yàn)研究院
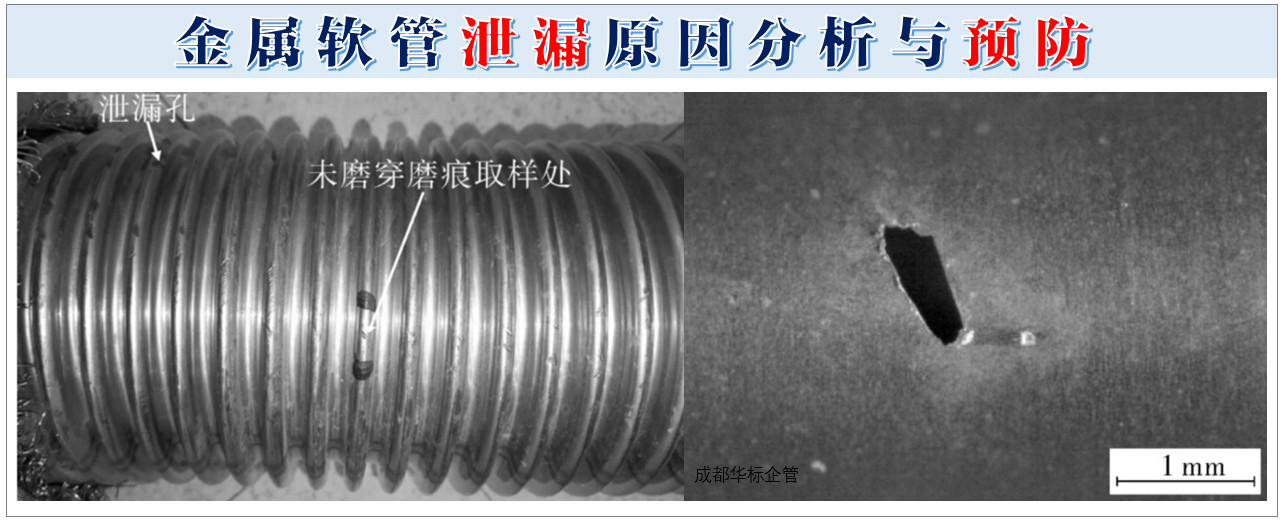
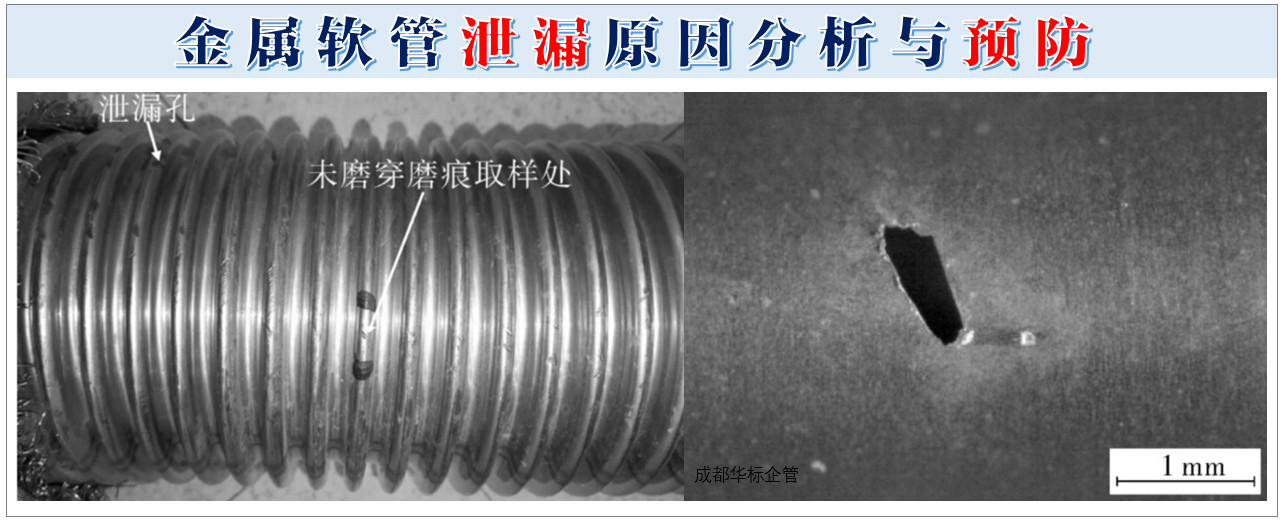
摘要:某核電設(shè)備上使用的金屬軟管在1年內(nèi)發(fā)生泄漏。采用掃描電鏡、光學(xué)顯微鏡、顯微硬度計(jì)等儀器對(duì)泄漏的金屬軟管進(jìn)行了宏觀和微觀檢驗(yàn)、硬度檢測(cè)及化學(xué)成分分析。結(jié)果表明,金屬軟管的泄漏是由鋼絲網(wǎng)套與波紋管發(fā)生摩擦引起的機(jī)械損傷導(dǎo)致的。同時(shí),提出了相應(yīng)的預(yù)防措施。
關(guān)鍵詞:金屬軟管;波紋管;鋼絲網(wǎng)套;犁痕;摩擦
0引言
某主泵冷卻水循環(huán)系統(tǒng)中使用的金屬軟管在1年內(nèi)發(fā)生了泄漏,圖1為使用單位采用氣密性試驗(yàn)查找出泄漏部位、將該部位附近的鋼絲網(wǎng)套去除后的金屬軟管的宏觀形貌。該金屬軟管在使用現(xiàn)場(chǎng)豎直方向S形彎曲安裝,兩頭法蘭連接,通徑DN80mm,長(zhǎng)度750mm,現(xiàn)場(chǎng)有三維震動(dòng),有效振動(dòng)加速度為水平2.1mm/s,垂直4.3mm/s,軸向8.5mm/s。工作壓力12bar,工作溫度75℃,介質(zhì)為除鹽水添加磷酸三鈉,pH值11~11.5。
該金屬軟管按GB/T14525—2010《波紋金屬軟管通用技術(shù)條件》[1]生產(chǎn)制備。波紋管材料為06Cr18Ni11Ti,壁厚0.3mm,固溶熱處理狀態(tài),材料標(biāo)準(zhǔn)為GB/T3280—2007《不銹鋼冷軋鋼板和鋼帶》[2];網(wǎng)套采用鋼絲編織而成,編織參數(shù)為64mm×14mm×0.4mm,材料為06Cr19Ni10,冷拉狀態(tài),材料標(biāo)準(zhǔn)為GB/T4240—2009《不銹鋼絲》[3]。
文中采用化學(xué)分析、硬度分析、宏觀及微觀檢驗(yàn)等方法,對(duì)該金屬軟管的泄漏失效原因進(jìn)行分析,并提出相應(yīng)的預(yù)防措施。
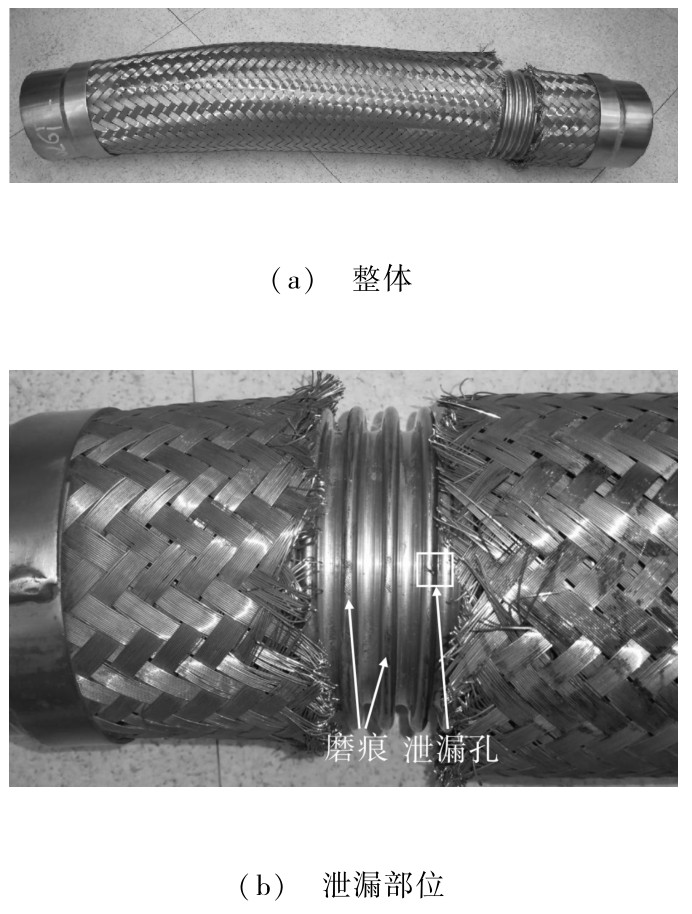
圖1泄漏金屬軟管宏觀形貌
1理化檢驗(yàn)
1.1宏觀檢驗(yàn)
1.1.1泄漏金屬軟管宏觀形貌
圖1示出泄漏金屬軟管及泄漏孔部位的宏觀形貌,該金屬軟管略呈彎曲弧形狀。泄漏孔位于波紋管波峰上,與波紋管的軸成45°,與外部網(wǎng)套的鋼絲編織方向一致,在泄漏孔附近有很多與鋼絲編織方向一致的磨痕,磨痕處呈黃褐色。泄漏孔附近的外部鋼絲網(wǎng)套有黃褐色銹跡。
去除泄漏金屬軟管的鋼絲網(wǎng)套,對(duì)鋼絲網(wǎng)套內(nèi)表面及波紋管進(jìn)行宏觀形貌觀察。
鋼絲網(wǎng)套內(nèi)表面的宏觀形貌如圖2所示??梢钥闯觯摻z表面有銹跡,局部不平整,沿著鋼絲的兩個(gè)編織方向有鋼絲凸出、翹曲現(xiàn)象。泄漏孔附近的鋼絲網(wǎng)套內(nèi)部的鋼絲翹曲、凸出的程度更大,有的鋼絲還發(fā)生錯(cuò)位折疊現(xiàn)象。將鋼絲網(wǎng)套展開,在其內(nèi)表面發(fā)現(xiàn)多處銹蝕部位存在磨痕。
波紋管的宏觀形貌如圖3所示??梢钥闯觯饘佘浌苷麄€(gè)波紋管段沿著軸向呈彎曲弧形狀,泄漏孔位于波紋管背彎面一側(cè)的波峰處。在泄漏孔附近的背彎面波峰上有許多磨痕,磨痕方向與波紋管軸向成45°,有的磨痕方向相互垂直,與外部鋼絲網(wǎng)套的編織方向一致。
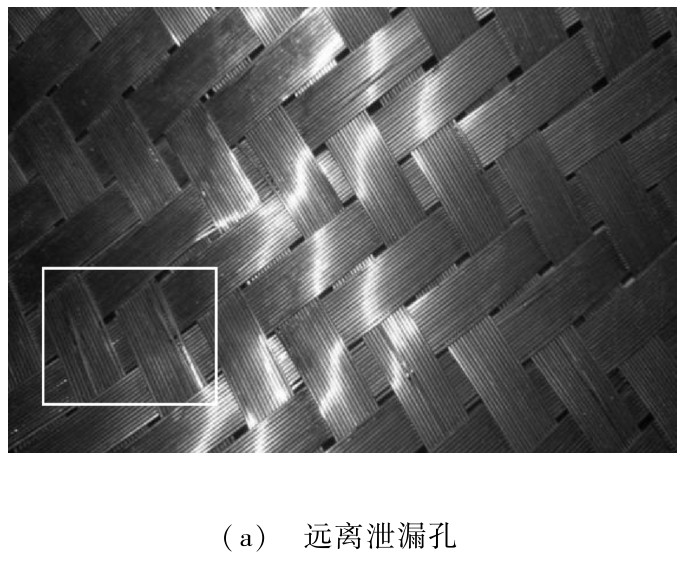

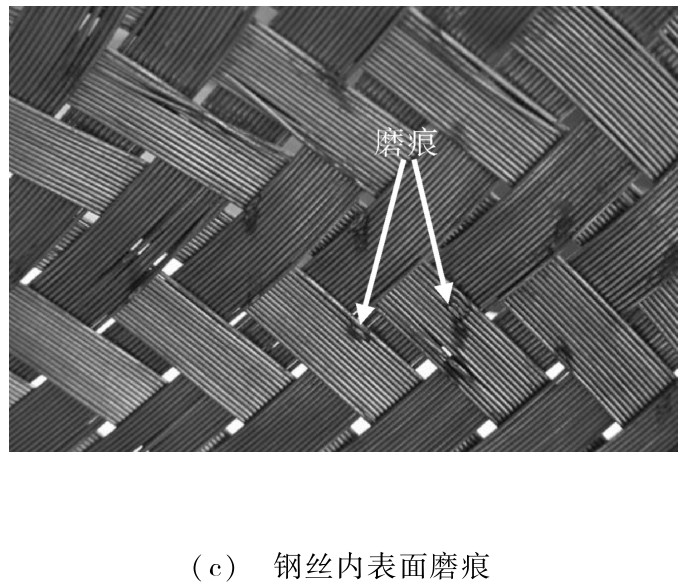
圖2鋼絲網(wǎng)套內(nèi)表面宏觀形貌
1.1.2波紋管泄漏孔、未磨穿磨痕、鋼絲網(wǎng)套內(nèi)表面磨痕宏觀形貌
在圖3所示的泄漏孔及未磨穿磨痕處分別取樣,采用體式顯微鏡對(duì)其進(jìn)行宏觀檢驗(yàn)。
泄漏孔的宏觀形貌如圖4所示??梢钥闯觯孤┛淄獗砻嬗悬S褐色斑,局部有被磨蹭的白亮層,泄漏孔兩頭開口較大,沿著一定的傾角逐漸延伸至內(nèi)表面;泄漏孔內(nèi)表面周圍區(qū)域光滑,在泄漏孔邊緣連著一條未完全脫離的金屬皮。
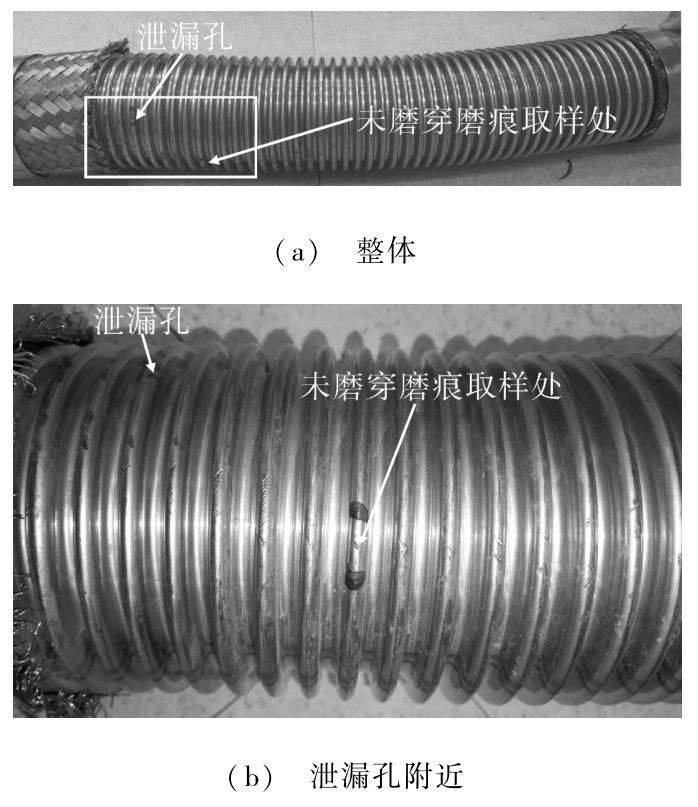
圖3波紋管的宏觀形貌
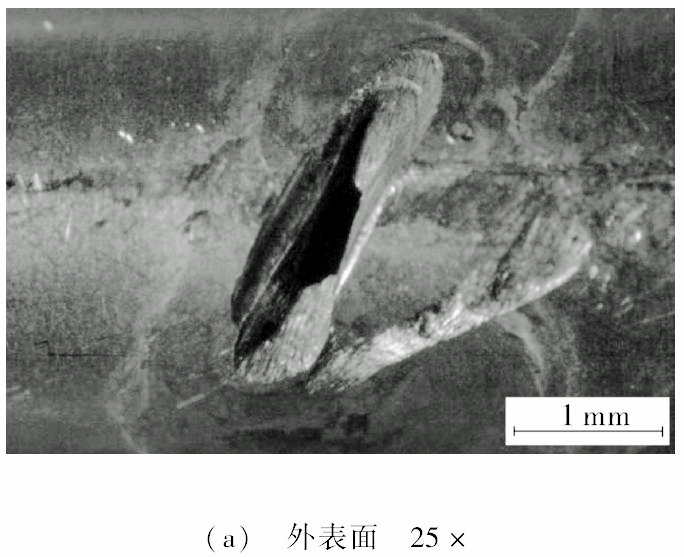
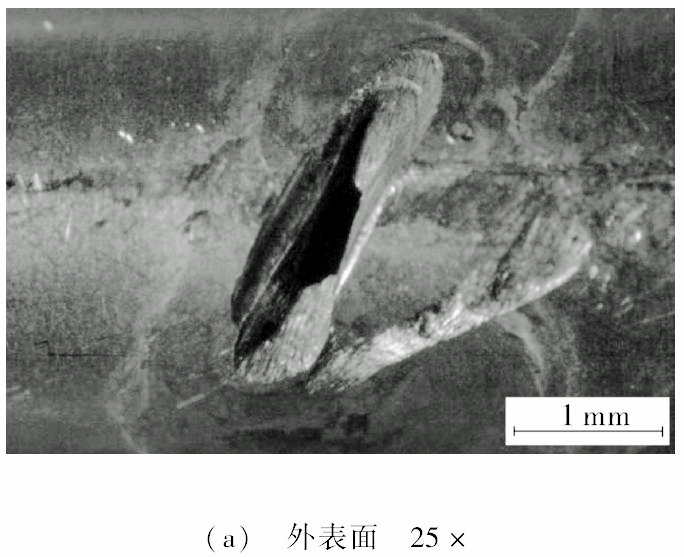
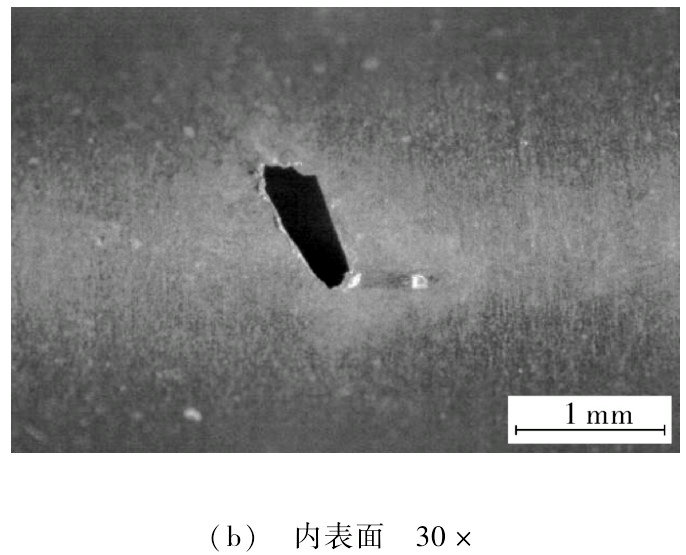
圖4泄漏孔的宏觀形貌
未磨穿磨痕的宏觀形貌如圖5所示??梢钥闯?,磨痕位于波紋管波峰外表面,沿著與波紋管軸向成45°方向上呈凹坑狀,凹坑內(nèi)部有與磨痕形成方向垂直的細(xì)微痕跡。
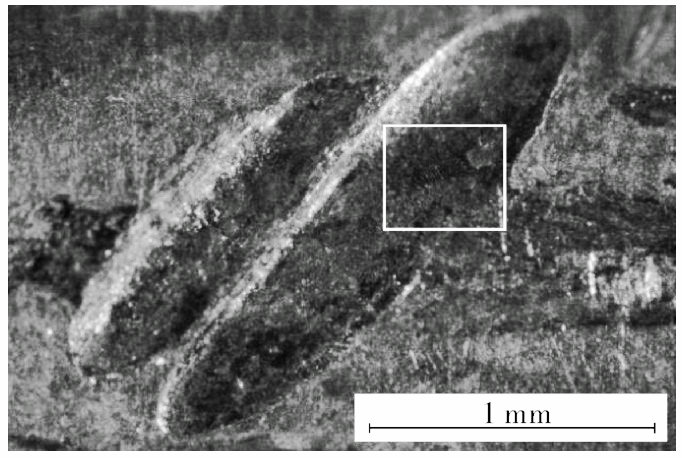
圖5未磨穿磨痕的宏觀形貌50×
在圖2(c)所示的鋼絲內(nèi)表面磨痕處取樣,采用體式顯微鏡對(duì)其進(jìn)行宏觀形貌觀察,從圖6中可以發(fā)現(xiàn)鋼絲內(nèi)表面有一定的磨損,鋼絲局部變形,呈扁平狀。
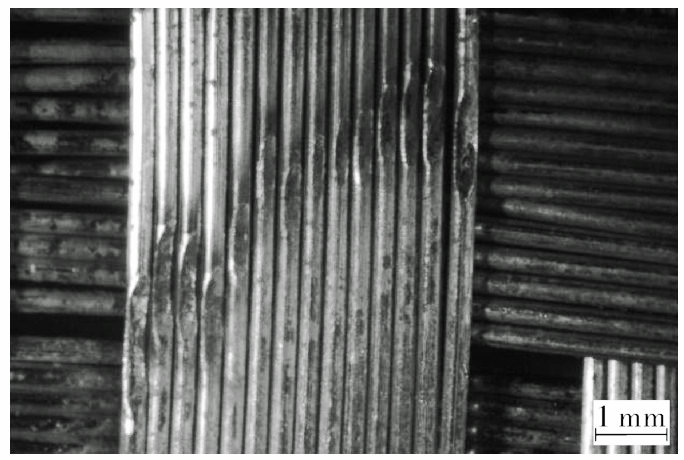
圖6鋼絲網(wǎng)套內(nèi)表面磨痕宏觀形貌10×
1.2化學(xué)成分分析
采用碳硫分析儀、電感耦合等離子體質(zhì)譜儀、分光光度儀對(duì)波紋管、鋼絲進(jìn)行化學(xué)成分分析,結(jié)果如表1所示。
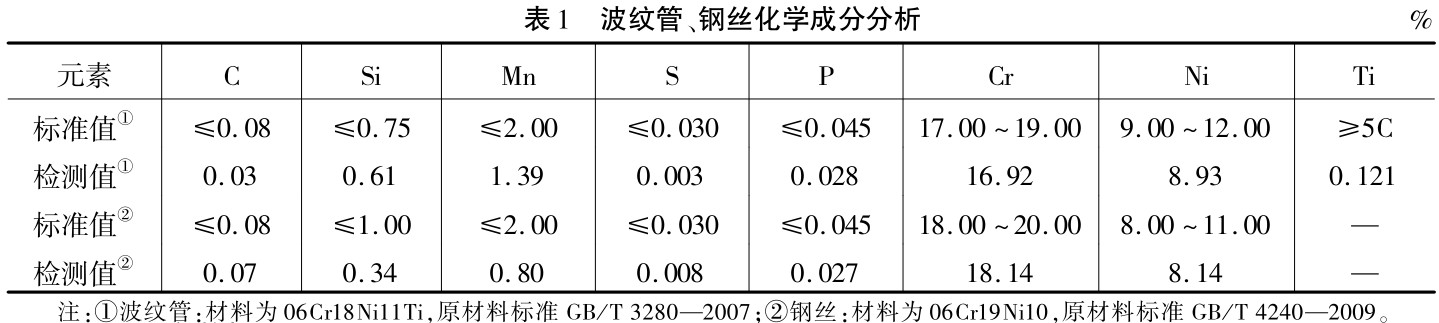
對(duì)照波紋管原材料標(biāo)準(zhǔn)GB/T3280—2007《不銹鋼冷軋鋼板和鋼帶》,其Cr,Ni,Ti含量偏低,但在GB/T222—2006《鋼的成品化學(xué)成分允許偏差》范圍內(nèi);對(duì)照鋼絲原材料標(biāo)準(zhǔn)GB/T4240—2009《不銹鋼絲》,鋼絲的化學(xué)成分合格。
1.3波紋管泄漏孔、未磨穿磨痕微觀形貌
采用掃描電鏡對(duì)圖4所示的泄漏孔內(nèi)外表面、圖5所示的未磨穿磨痕進(jìn)行微觀形貌觀察。
泄漏孔的內(nèi)外表面的微觀形貌如圖7所示。
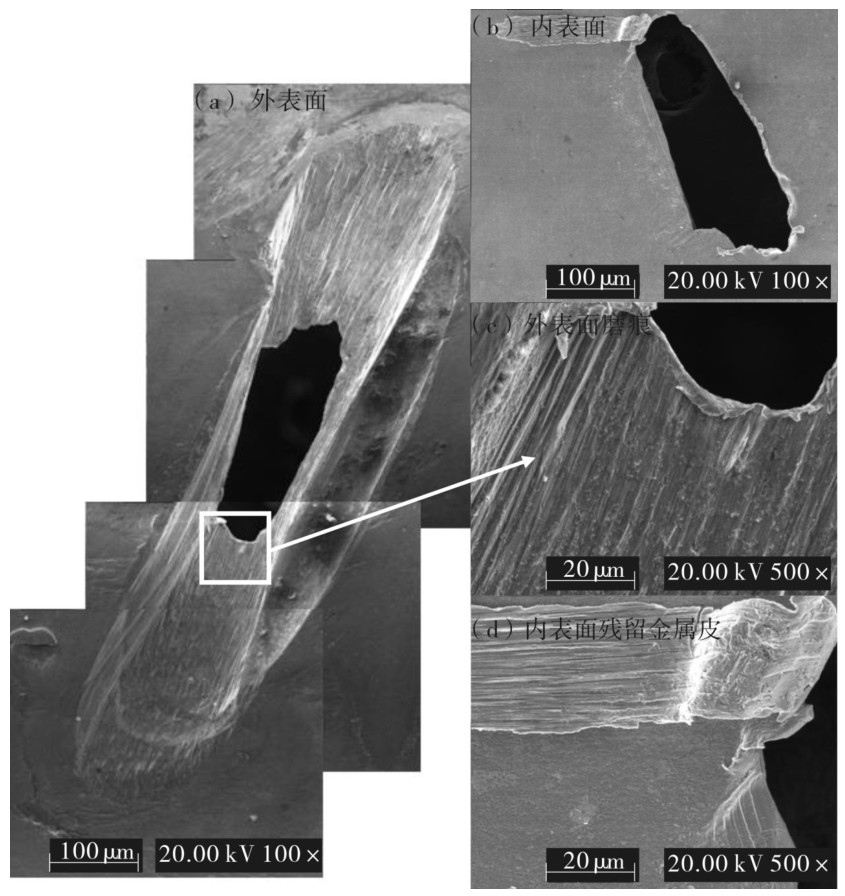
圖7(a)示出泄漏孔外表面的磨損形貌,泄漏孔兩頭留下沿著一個(gè)方向傾斜的條帶,條帶細(xì)窄且密集分布,將條帶放大至500倍可見一條條的犁痕及深淺不一的犁溝,屬典型的機(jī)械損傷形貌[4-5]。
整個(gè)泄漏部位內(nèi)表面周圍比較光滑,泄漏孔上面連著一條未完全撕裂的金屬皮,上面布滿縱向的條帶,其方向與外表面兩頭區(qū)域的條帶方向一致。泄漏孔邊緣金屬向內(nèi)表面翹起。
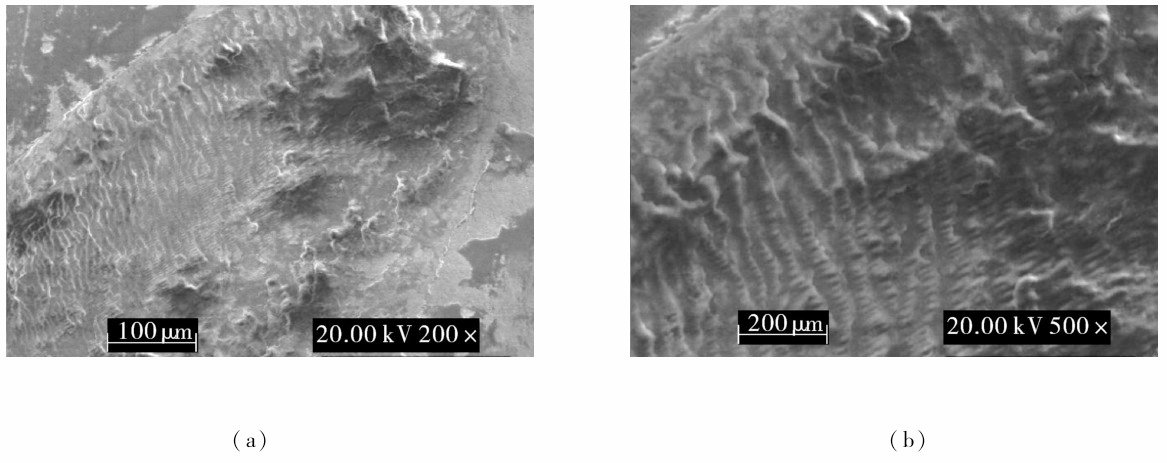
圖8未磨穿磨痕微觀形貌
未磨穿磨痕的微觀形貌如圖8所示,磨痕內(nèi)部有斷續(xù)狀的細(xì)微弧形臺(tái)階,呈魚鱗狀,是在磨痕形成過程中沿著磨痕形成方向及與磨痕形成方向垂直的兩個(gè)方向逐漸擠壓堆積而成的痕跡。
1.4能譜分析
對(duì)泄漏孔附近內(nèi)外表面、未磨穿磨痕進(jìn)行能譜分析。泄漏孔內(nèi)外表面的分析結(jié)果如圖9及表2、圖10及表3所示,在泄漏孔外表面的磨痕頭部(譜圖3)有大量氧元素存在,外表面有少量氟、硫腐蝕性元素存在,泄漏孔內(nèi)表面有少量氟元素。未磨穿磨痕的分析結(jié)果如圖11及表4所示,磨痕內(nèi)部有大量氧元素存在。可見波紋管外表面的氧、氟元素的含量高于其內(nèi)表面相應(yīng)元素的含量。
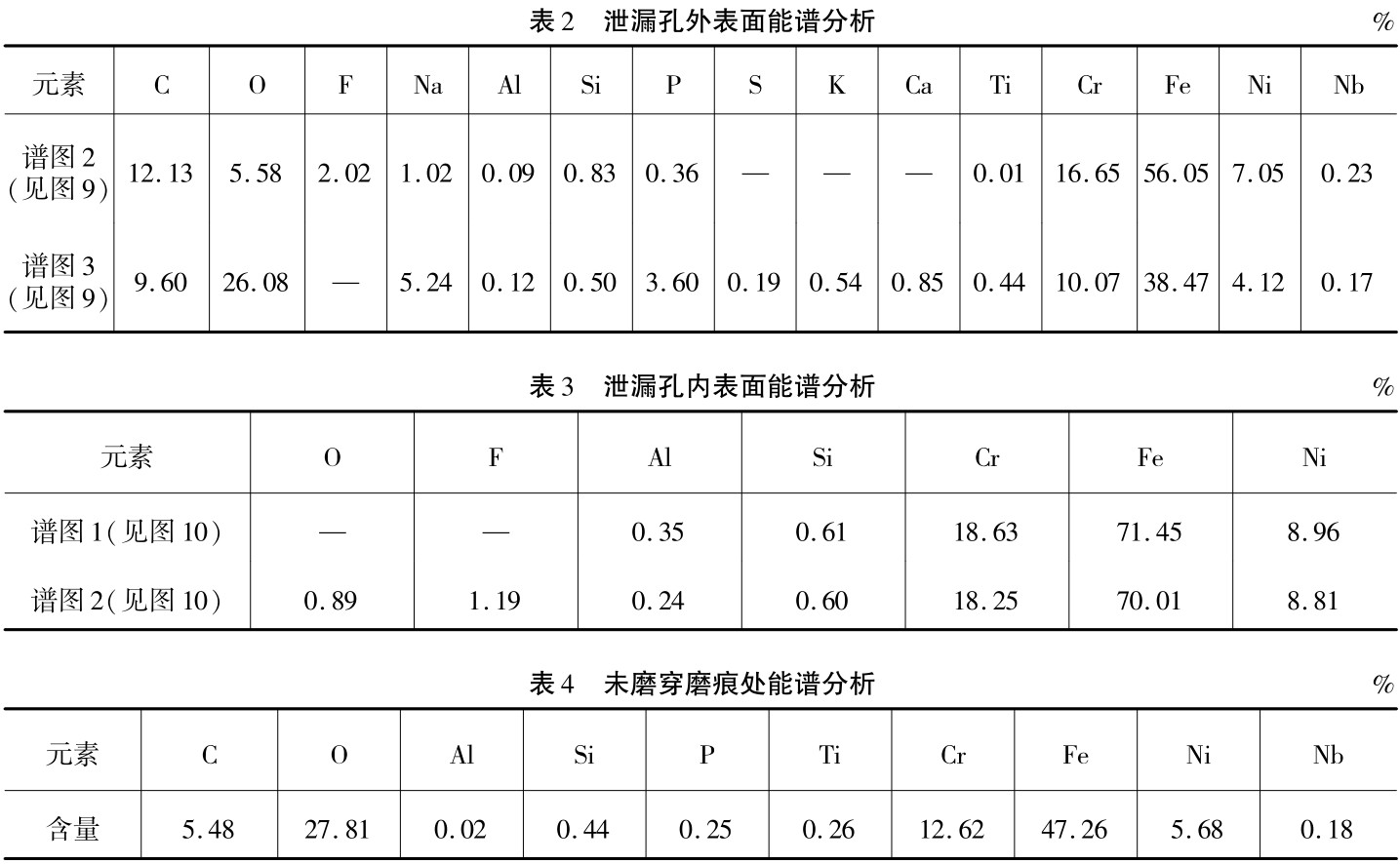
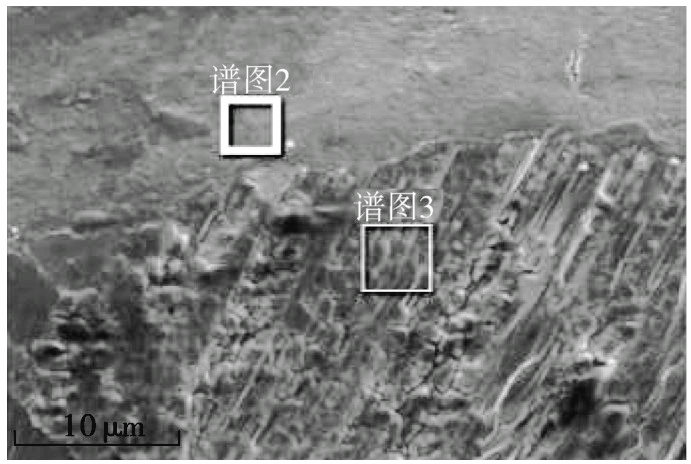
圖9泄漏孔外表面
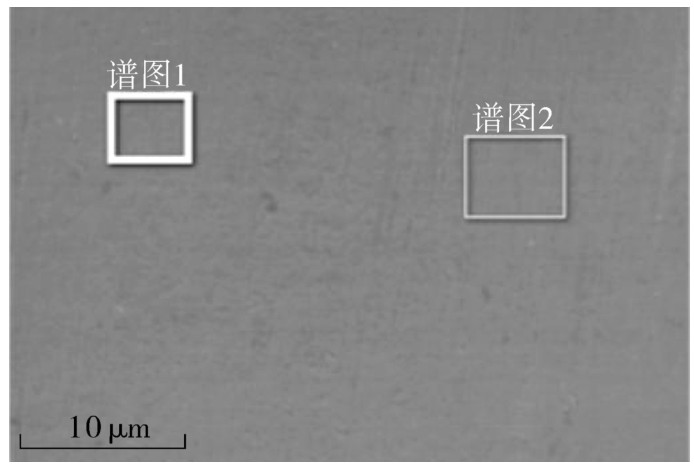
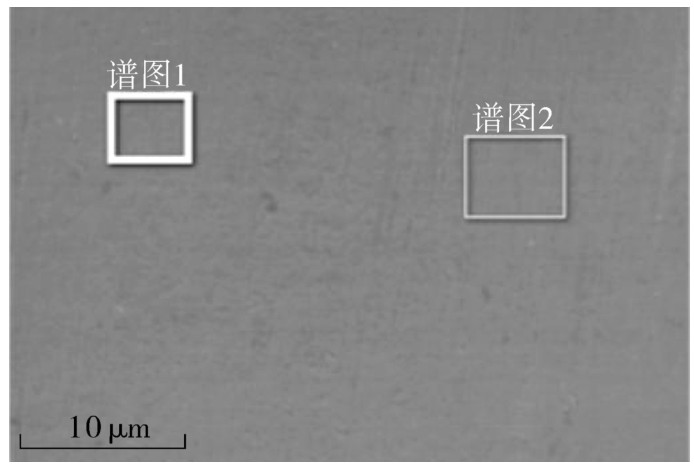
圖10泄漏孔內(nèi)表面
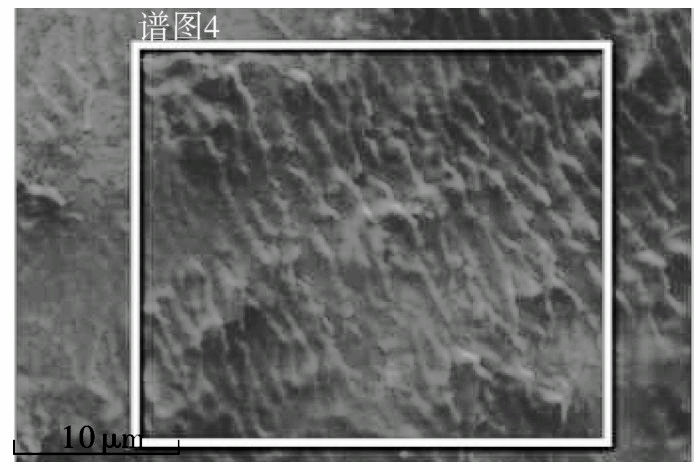
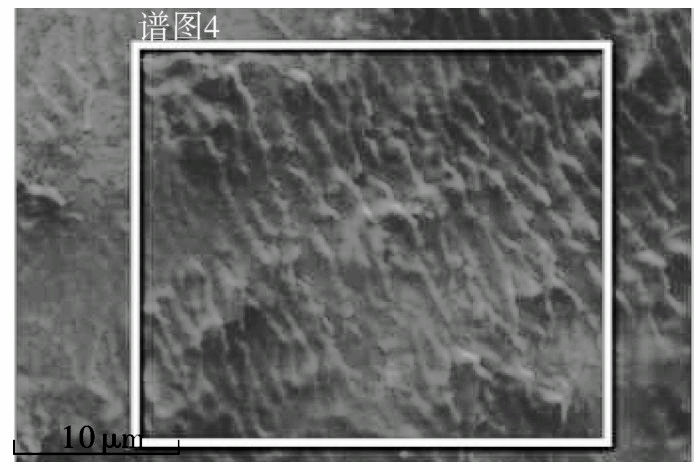
圖11未磨穿磨痕處
1.5硬度分析
在波紋管磨痕處截取波峰橫截面試樣、波谷橫截面試樣,在鋼絲網(wǎng)套上隨機(jī)截取7根鋼絲。在熱鑲嵌磨拋后進(jìn)行顯微維氏硬度試驗(yàn)(HV0.05),結(jié)果如表5所示,波紋管的硬度比鋼絲的硬度低。
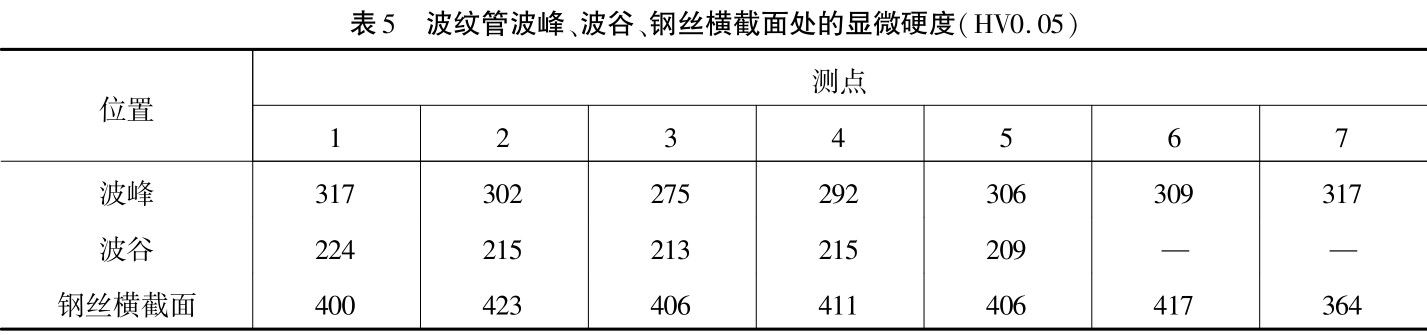
1.6金相組織
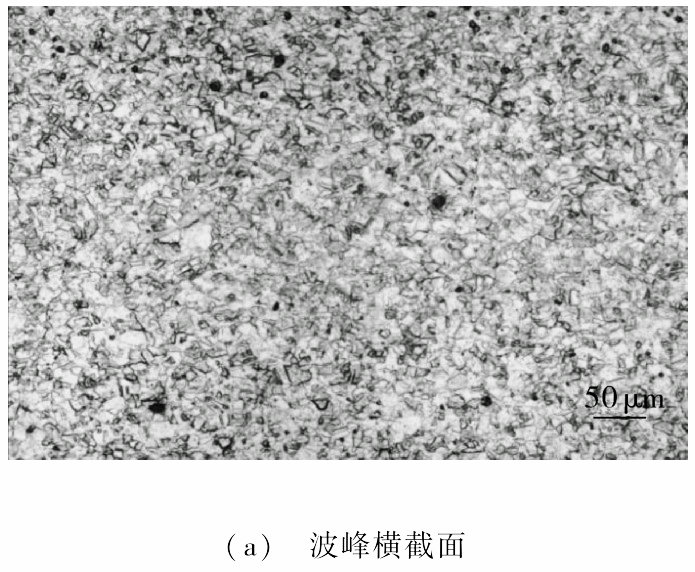
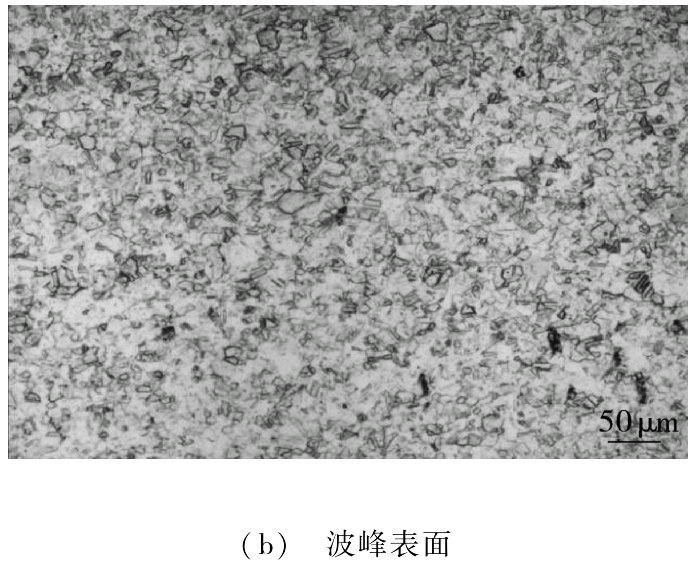
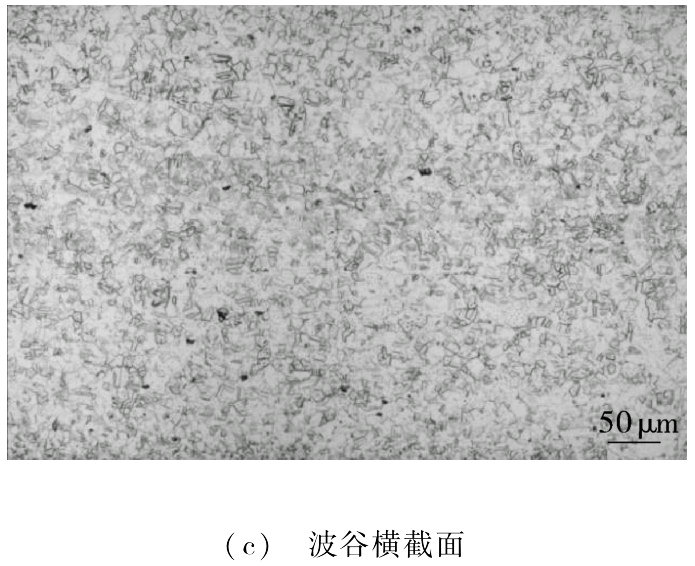
圖12波紋管的金相組織200×
波峰橫截面、表面金相組織和波谷橫截面組織如圖12所示,均為典型的奧氏體組織,晶內(nèi)有攣晶。在金相組織中發(fā)現(xiàn)少量氮化物夾雜。
2 分析與討論該金屬軟管的波紋管壁厚極?。?.3mm),在三維振動(dòng)的環(huán)境下使用了一年發(fā)生泄漏。經(jīng)檢驗(yàn)后發(fā)現(xiàn)泄漏金屬軟管的波紋管呈彎曲弧形狀,在波紋管的背彎面一側(cè)的波峰外表面處發(fā)現(xiàn)泄漏孔,泄漏孔附近的背彎面多處發(fā)現(xiàn)磨痕,其方向均與外表面的網(wǎng)套編織的兩個(gè)垂直的方向一致;鋼絲網(wǎng)套內(nèi)表面有凸出、翹曲及錯(cuò)排等不平整現(xiàn)象,且鋼絲內(nèi)表面局部有一定的磨損,呈扁平狀。
泄漏孔外表面存在被磨蹭的白亮層,兩頭開口較大,沿著一定的傾角逐漸延伸至內(nèi)表面,邊緣金屬向內(nèi)表面翹曲。泄漏孔外表面邊緣處與內(nèi)表面殘留金屬皮的微觀形貌一致,為典型的犁痕形貌,屬機(jī)械損傷。波紋管的未磨穿磨痕的微觀形貌呈魚鱗狀,有細(xì)微弧形臺(tái)階,是在磨痕形成過程中沿著磨痕形成方向及與磨痕形成方向垂直的兩個(gè)方向逐漸擠壓堆積而成的痕跡。泄漏孔外表面的氧含量遠(yuǎn)大于內(nèi)表面的含量,未磨穿磨痕處的氧含量也較高,可推斷泄漏孔附近區(qū)域外表面的氧含量大于內(nèi)表面的含量。波紋管的硬度低于鋼絲的硬度。
綜上所述,可推斷泄漏金屬軟管在運(yùn)行過程中,鋼絲內(nèi)表面與發(fā)生彎曲的波紋管發(fā)生相互摩擦,在波紋管波峰外表面留下摩擦磨痕,直至磨穿發(fā)生泄漏為止。泄漏金屬軟管的運(yùn)行條件(三維有效振動(dòng)加速度較低)、波紋管泄漏孔內(nèi)外表面的微觀形貌中發(fā)現(xiàn)典型的犁痕形貌、犁溝現(xiàn)象,未磨穿磨痕表面微觀形貌中發(fā)現(xiàn)的擠壓堆積痕跡,符合微動(dòng)磨損的發(fā)生條件[4,6-8]。
3結(jié)語
該金屬軟管泄漏失效是由波紋管與鋼絲網(wǎng)套摩擦導(dǎo)致的機(jī)械損傷。為了避免以后這類摩擦導(dǎo)致的磨損泄漏事故的再次產(chǎn)生,建議如下。
(1)優(yōu)化金屬軟管的制造工藝,加強(qiáng)對(duì)鋼絲網(wǎng)套的外觀檢驗(yàn),避免出現(xiàn)網(wǎng)套表面不平整、斷絲、折疊、凸出、翹曲等現(xiàn)象[1,7-8];
(2)改善金屬軟管的現(xiàn)場(chǎng)安裝條件,應(yīng)保證順其自然直線安裝,不應(yīng)任意壓縮彎曲呈“~”形安裝[9-10]。
參考文獻(xiàn):
[1]GB/T14525—2010,波紋金屬軟管通用技術(shù)條件[S].
[2]GB/T3280—2007,不銹鋼冷軋鋼板和鋼帶[S].
[3]GB/T4240—2009,不銹鋼絲[S].
[4]張棟,鐘培道,陶春虎,等.失效分析[M].北京:國(guó)防工業(yè)出版社,2008:241-253.
[5]劉杰英.磨損失效分析案例匯編[M].北京:機(jī)械工業(yè)出版社,2005.
[6]徐松.金屬材料磨損失效及防護(hù)的探討[J].現(xiàn)代經(jīng)濟(jì)信息,2010(1):217.
[7]陳建敏,周惠娣.磨損失效與摩擦學(xué)新材料的研究與發(fā)展[J].材料保護(hù),2004,37(7):35-39.
[8]杜健,李延夫,李曉旭,等.金屬軟管失效模式及失效原因分析[J].管道技術(shù)與設(shè)備,2015(3):1-3.
[9]齊艷麗,袁夕君,張金平,等.核電廠設(shè)備冷卻水系統(tǒng)金屬軟管使用中存在的問題及對(duì)策研究[J].機(jī)械,2012(9):73-77.
[10]郭兆海.石油儲(chǔ)罐進(jìn)出口管段用抗震金屬軟管[J].管道技術(shù)與設(shè)備,1998(2):30-32.
收稿日期:2017-11-01修稿日期:2018-01-25
作者簡(jiǎn)介:陳彩霞(1981—),女,高級(jí)工程師,主要從事理化檢測(cè)和失效分析工作,通信地址:211178江蘇省南京市江寧濱江經(jīng)濟(jì)開發(fā)區(qū)喜燕路18號(hào),E-mail:jenifer0108@163.com。
? 如果本文對(duì)您有幫助,請(qǐng)分享給您的朋友!
【提示】:
1.不斷更新的好資料和答疑集錦在 gd919.cn “找資料”欄目公布。
2.QQ群:2300+人群,專業(yè)高質(zhì)、答疑解惑、互動(dòng)交流,Q群名:中國(guó)設(shè)備管理, Q群號(hào): 283752911
主要交流:設(shè)備管理體系標(biāo)準(zhǔn)、ISO55001資產(chǎn)管理、設(shè)備完整性管理、6S管理、目視管理、安全管理、企業(yè)管理等,純廣告者禁入!
3.加"中國(guó)設(shè)備管理" Q群,總有一個(gè)人知道你問題的答案!
4.優(yōu)秀留言有機(jī)會(huì)錄入“找資料”欄目答疑集錦,并歡迎大家來稿分享